- Prune
- Posts
- Shaker legacies pt. 2
Shaker legacies pt. 2
Thomas Moser's road not traveled.
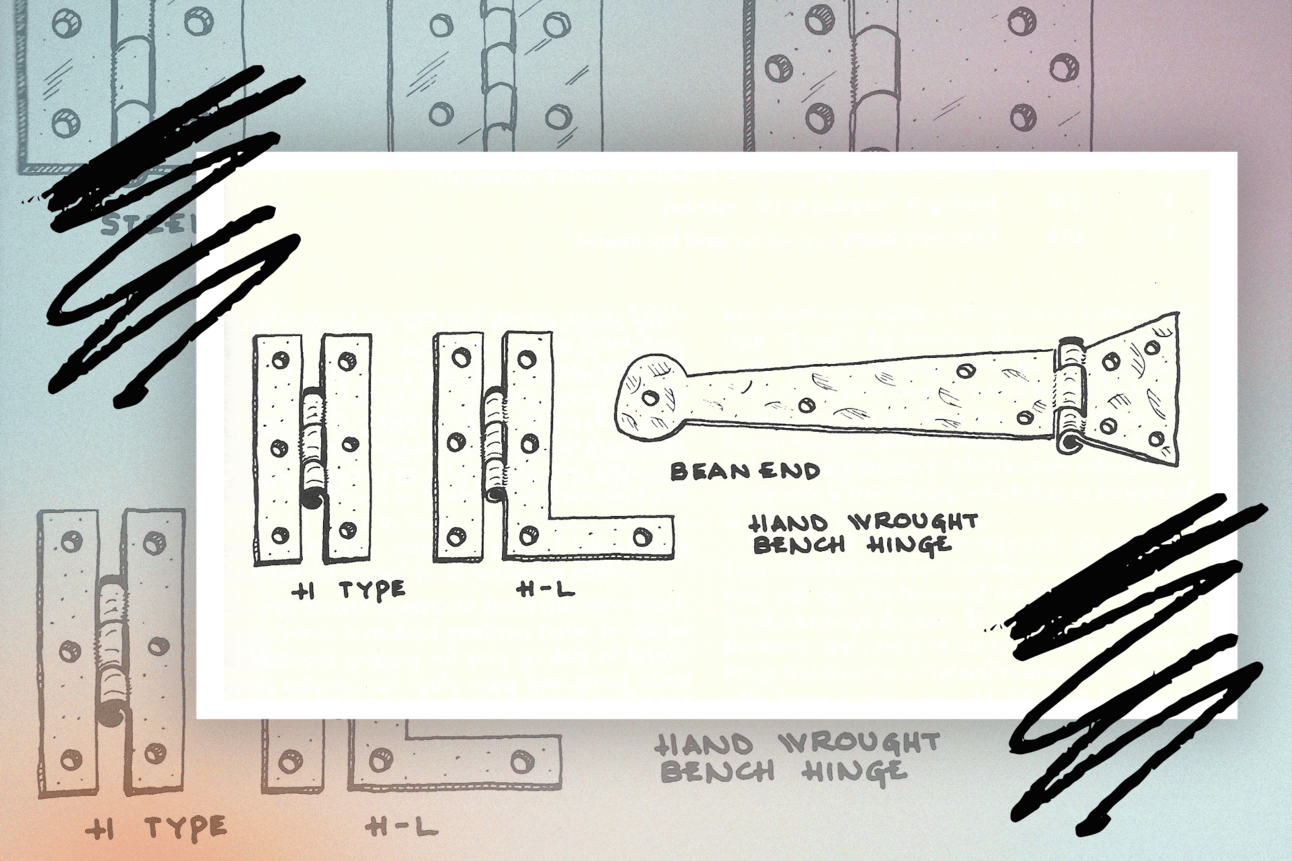
This is part two of a two-part series by Sam Wells on the late furniture maker Thomas Moser. You can read part one here.
Perhaps the most valuable part of Moser’s 1977 book How to Build Shaker Furniture is its pen and ink measured drawings and illustrations, carried out by then Moser employee Christian Becksvoort. Becksvoort’s career is evidence that alternate destinies are still possible when it comes to unscaled operations.
After graduating from college in 1972 with a forestry degree, Becksvoort worked in Maryland as a wildlife researcher. He became obsessed with Shaker furniture after seeing the 1973 Shaker show at the Renwick in D.C., and moved to Maine shortly after, where he began to work for Thos. Moser. After nine years there, he left and went on to start a one-man furniture business out of a shop on a dirt road in New Gloucester, Maine.
Now in his late seventies, Becksvoort stopped taking commissions after breaking his wrist in 2022. By his own count, 977 pieces left his shop in his 38 years in business (an average of 26 pieces a year), and he still "designed, laid out, glued up, sanded, constructed and finished" each piece by himself until the end.

By the 1990s, as this article in Fine Woodworking attests, Thomas Moser’s very status as a woodworker had been brought into question. He was seen by large parts of the woodworking world as a sellout for automating so much work while claiming to be doing the same thing as the one man shops.
More than anything, this conflict stemmed from the complicated and difficult-to-scale problem of carving out chair seats for Moser’s signature piece, the Continuous Arm Chair. The seats of windsor, or more broadly stick chairs, are traditionally sculpted into what Chairmaker Peter Galbert calls their “un-namable shape” by a succession of increasingly precise (and specific to the task) hand tools, progressing from an adze to a scorp to a travisher and beyond until the seat reaches its desired shape and smoothness, and because of this, their seats are generally made of softwoods.
He was seen by large parts of the woodworking world as a sellout for automating so much work while claiming to be doing the same thing as the one man shops.
Moser, as is the case with many “fine” furniture makers, stopped using pine or other softwoods a few years into the business because they are seen as cheap. He was moving away from hand tools anyway in the late 70s, so had to come up with a series of solutions to perfectly recreate this landscape of subtle curves in cherry.
After a decade of stopgap solutions, one of which involved rotating a seat blank the wrong way (perpendicular) across the blade of a table saw and finishing the rough shaping with a chainsaw, Moser found his solution in the world of aircraft manufacturing. In 1987, Moser bought a five-axis computerized milling machine (great demonstration of a smaller-scale version of this process starting at 8:43 of this video) that had been previously used to mill out the wings of fighter jets from blocks of metal. The precision and efficiency of this machine allowed Thos. Moser to shift away from more traditional, rectilinear forms in an effort to create furniture that was more obviously “Moser” and was harder to copy.